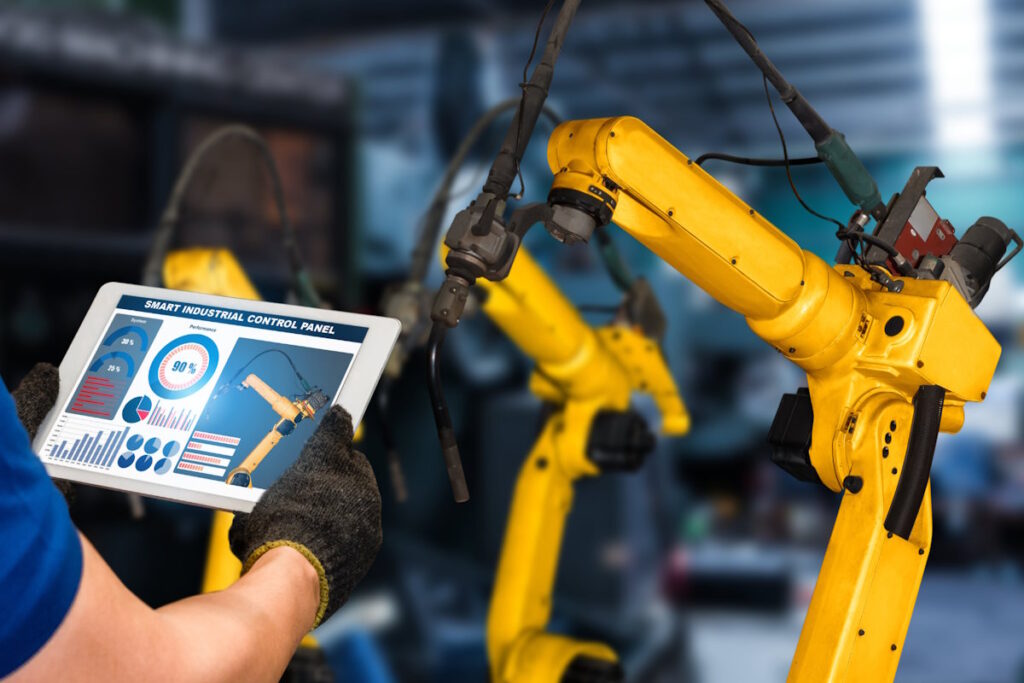
Adapting to the Future of Manufacturing: Trends and Technologies
Trends and Technologies
The manufacturing industry is undergoing a profound transformation due to new emerging technologies and shifts in global economic dynamics. As demand for customized products, faster production, and greater efficiency increases, businesses must find ways to keep up. To stay competitive and sustainable, manufacturers need to adapt to these changes by embracing emerging technologies and new trends. This will help them meet evolving customer needs and stay ahead in a rapidly changing market.
Let’s look at the key innovations and trends shaping the future of manufacturing and how businesses can adapt to the upcoming challenges and opportunities.
The Rise of Smart Manufacturing
The future of manufacturing centers around smart manufacturing, which leverages advanced technologies like the Internet of Things (IoT), big data, artificial intelligence (AI), and cloud computing. These technologies create production environments that are more efficient, flexible, and adaptable, enabling businesses to quickly respond to changing demands and improve overall performance. They also enable manufacturers to monitor and control production processes in real-time, ensuring operations are precise, responsive, and adaptable to changes.
IoT plays a key role in smart manufacturing by connecting machines, sensors, and devices across the factory floor, enabling them to communicate with each other. This connectivity allows manufacturers to perform predictive maintenance, reduce downtime, and keep equipment running smoothly. With IoT-enabled sensors, manufacturers can monitor factors such as temperature, humidity, and machine wear, enabling timely maintenance before costly failures occur.
AI and machine learning are crucial to smart manufacturing because they allow machines to analyze data and make decisions in real-time. For instance, AI predicts demand fluctuations, helping manufacturers adjust production schedules proactively. Machine learning also optimizes production by identifying inefficiencies and recommending improvements.
Additive Manufacturing: 3D Printing Revolution
Additive manufacturing, also known as 3D printing, has emerged as one of the most exciting trends in manufacturing. Unlike traditional methods, which often cut, drill, or shape material from a larger block, 3D printing builds parts by adding material layer by layer based on a digital model. This process enables the creation of more complex shapes that traditional techniques find difficult or impossible to achieve. It offers several key advantages, such as reduced material waste, faster prototype production, and greater design flexibility, which facilitates customization and quicker design adjustments.
As consumer demand grows for personalized products, 3D printing helps manufacturers make small batches of custom items at lower costs than traditional methods. This is especially useful in industries like healthcare, where custom prosthetics or implants are often needed.
3D printing also simplifies supply chains. Traditional manufacturing relies on sourcing materials from multiple suppliers, causing delays and high costs. With 3D printing, manufacturers can produce parts on demand, reducing the need for large inventories and outside suppliers. This shift promotes more localized production and changes the way global supply chains work.
Automation and Robotics
Automation has been a vital part of manufacturing for decades, but recent advancements in robotics and automation technology are taking it to new levels. Robots are becoming more advanced, performing more than just repetitive tasks. Collaborative robots, or “cobots,” now work together with humans on the factory floor. They handle tasks like assembly, material handling, and inspection with high precision.
By integrating AI and machine vision, robots can learn from their environment and adapt to new tasks. This flexibility allows them to quickly switch between tasks and work with different materials or product designs. For example, robots now perform quality control checks, detecting defects that human inspectors might miss.
Robots and automation also help reduce labor costs and solve workforce shortages. Automated systems can work around the clock, ensuring continuous production. This not only boosts productivity but also meets the demand for faster production cycles.
Artificial Intelligence and Machine Learning
Artificial intelligence (AI) and machine learning (ML) are transforming the manufacturing sector. AI helps machines analyze large amounts of data, detect patterns, and make decisions with minimal human intervention. In the manufacturing industry, AI is used to optimize everything from inventory management and supply chain logistics to product quality and maintenance schedules.
For example, AI can predict machine failures by analyzing data from IoT sensors, allowing manufacturers to schedule maintenance and avoid costly downtime. In quality control, AI-powered vision systems inspect products for defects much faster and more accurately than humans.
Machine learning enables predictive analytics, using data to forecast demand, identify inefficiencies, and optimize supply chains. By analyzing historical data, manufacturers can adjust operations to align with market trends and customer needs. This capability helps manufacturers respond to disruptions like supply chain issues or unexpected shifts in demand.
Sustainability and Green Manufacturing
Sustainability is now a key focus in the manufacturing sector. Companies are becoming more aware of the environmental impact of their operations and are investing in green technologies to lower their carbon footprint. This shift is driven not only by rising consumer demand for eco-friendly products but also by stricter environmental regulations from governments.
One important aspect of sustainable manufacturing is adopting energy-efficient technologies. Advanced systems powered by AI and IoT help reduce energy consumption by optimizing production processes in real time. For example, smart factories can adjust lighting, heating, and cooling based on the real-time needs of the production environment, cutting down on unnecessary energy use.
Circular economy principles are also gaining popularity. This approach aims to minimize waste and maximize the reuse and recycling of materials. Manufacturers are designing products with longer lifecycles and easier recyclability, while also finding ways to repurpose waste materials into new products. Additive manufacturing, especially 3D printing, plays a key role in this shift by allowing more precise use of raw materials and reducing waste during production.
The Role of the Workforce in the Future of Manufacturing
As manufacturing is becoming more and more automated and digitized, the workforce has a hard time adapting to these changes. Many even fear that automation will lead to job losses, but the situation is actually more complex. The future of manufacturing will likely require new skills, with increased demand for workers who can operate and maintain advanced technologies like robotics, AI, and 3D printing.
Workers must update their skills in data analysis, software programming, and robotics to stay competitive in the evolving manufacturing landscape. The rise of collaborative robots will create a need for human workers to supervise and interact with machines. This transformation provides opportunities for workers to upskill and reskill in a technology-driven environment.
Training and education will be crucial in preparing the workforce for the future. Manufacturers must invest in programs that teach workers how to operate and manage advanced technologies. Meanwhile, governments and educational institutions should collaborate to create pathways that help workers gain the skills necessary for future jobs.
The Digital Twin and Virtual Reality
The concept of the digital twin is rapidly gaining popularity in the manufacturing sector. A digital twin is a virtual replica of a physical product, process, or system. By simulating real-world conditions, manufacturers can test new designs, predict performance, and identify potential issues before they occur in the real world.
In manufacturing, companies use digital twins to model entire production lines or supply chains, helping them optimize operations and fix problems in real-time. When combined with virtual reality (VR) and augmented reality (AR), digital twins offer powerful tools for engineers and designers to visualize and interact with complex systems in a virtual space. This leads to more efficient product development cycles and faster time-to-market.
In conclusion, transformative technologies and trends are shaping the future of manufacturing. Innovations like smart manufacturing, 3D printing, AI, robotics, and sustainability efforts can improve efficiency and open new opportunities for customization, sustainability, and workforce development. These technologies facilitate companies to produce more tailored products, reduce waste, and create more sustainable processes.
As companies embrace these advancements, they must also be prepared to invest in technology, upskill their workforce, and adapt to an increasingly dynamic global market. The manufacturers who successfully navigate these changes will position themselves to succeed and lead in the future of manufacturing.