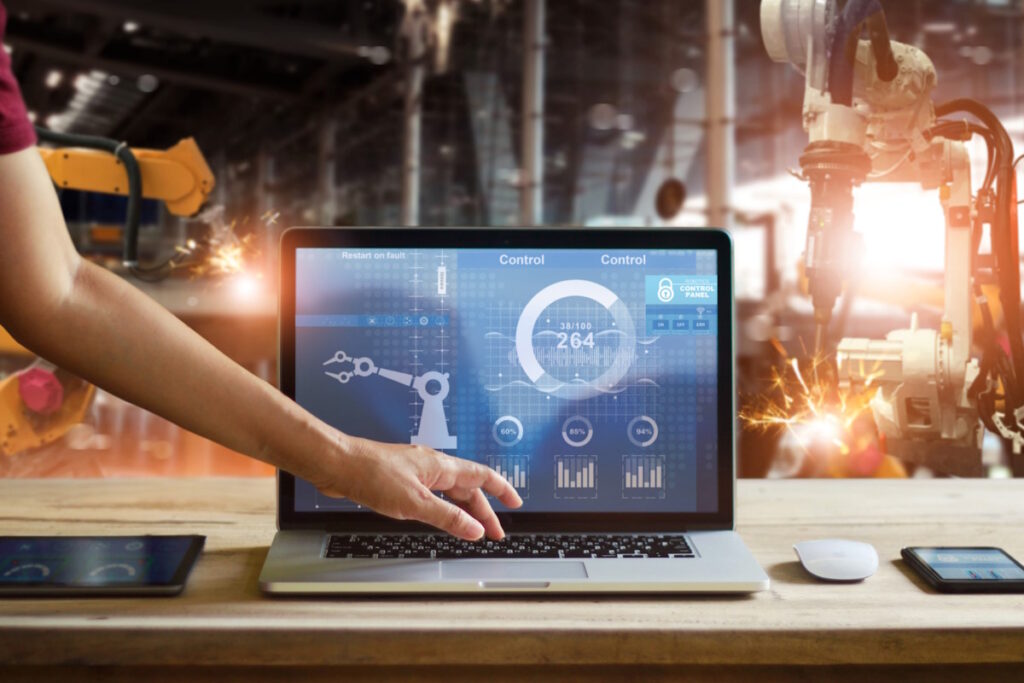
Digital Twins In Manufacturing:
Optimizing Production And Efficiency
In the modern world of manufacturing, companies face constant pressure to increase productivity, reduce costs, and enhance product quality. One of the most promising technological advancements in the industry today is the use of Digital Twins. This innovative technology has the potential to transform the way manufacturers design, operate, and maintain their production systems. By creating digital replicas of physical objects or processes, Digital Twins offer a powerful tool to optimize production and improve efficiency across all aspects of manufacturing.
What is a Digital Twin?
A Digital Twin is a computer-generated duplicate version of a real-world object, system, or method. It uses real-time data, sensors, and advanced analytics to mirror the behavior and performance of its physical counterpart. In simple terms, it functions as a link between the physical and digital domains. For instance, in a manufacturing setting, a Digital Twin could represent a machine, a production line, or even an entire factory. By simulating the physical system in a digital environment, manufacturers can monitor, analyze, and predict its behavior without needing to rely solely on the physical world.
How Digital Twins Work in Manufacturing
To create a Digital Twin, manufacturers first collect data from physical assets using sensors and IoT devices. This data includes information about temperature, pressure, speed, vibration, and other critical parameters. The data is transmitted to a digital platform where it is processed and analyzed. Using advanced algorithms, machine learning, and artificial intelligence (AI), the Digital Twin is able to simulate the behavior of the physical system in real-time. As a result, manufacturers can gain valuable insights into the performance of their equipment, identify potential issues before they occur, and optimize their processes.
Important Features of Digital Twins in the Manufacturing Sector
- Data Collection
The first step in creating a Digital Twin is gathering data from sensors and other IoT devices embedded in the physical system. These sensors monitor various aspects of the system’s performance and transmit the data to the digital platform.
- Modeling and Simulation
Once the data is collected, it is used to create a virtual model of the physical system. This model is designed to replicate the behavior and dynamics of the real-world asset as accurately as possible. Simulation tools and software are used to perform various tests and scenarios on the Digital Twin, providing valuable insights into how the system will respond under different conditions.
- Analytics and Insights
After the Digital Twin is created, manufacturers can use advanced analytics to interpret the data and extract meaningful insights. This could involve identifying inefficiencies, predicting maintenance needs, or improving production processes. Ongoing data analysis allows manufacturers to refine their operations and make well-informed decisions.
- Real-Time Monitoring
One of the key benefits of Digital Twins is their ability to provide real-time monitoring of the physical system. As the Digital Twin is constantly updated with live data from sensors, it can offer a real-time view of the performance and status of the system. This empowers manufacturers to promptly detect anomalies and take necessary actions to resolve them while preventing issues from deteriorating.
Benefits of Digital Twins in Manufacturing
The implementation of Digital Twins in manufacturing offers a wide range of benefits that can significantly improve production efficiency, reduce downtime, and enhance overall performance.
- Improved Predictive Maintenance
Digital Twins are valuable for their potential to enhance predictive maintenance. In traditional manufacturing, maintenance is often performed on a fixed schedule, regardless of whether it’s needed. This strategy can cause both unnecessary disruptions and unforeseen failures.
With Digital Twins, manufacturers can move from a reactive maintenance strategy to a more proactive, data-driven approach. By continuously monitoring the condition of equipment and analyzing performance data, the Digital Twin can predict when a machine is likely to fail or require maintenance. This allows manufacturers to schedule maintenance activities only when needed, minimizing downtime and reducing the costs associated with unnecessary repairs.
- Enhanced Product Quality
Digital Twins also play a crucial role in ensuring product quality. By simulating production processes in a virtual environment, manufacturers can identify potential issues before they impact product quality. This might involve detecting variations in materials, changes in environmental conditions, or inefficiencies in the production process. With this insight, manufacturers can adjust their operations to ensure that the final products meet the highest quality standards.
For example, in a car manufacturing plant, a Digital Twin could help identify areas where imperfections in the assembly line might lead to defects in the finished product. By addressing these issues in real-time, manufacturers can improve product quality, reduce scrap rates, and ensure that customers receive high-quality products.
- Optimization of Production Processes
Digital Twins can help manufacturers optimize their production processes by providing insights into how different elements of the system interact. By analyzing data from the Digital Twin, manufacturers can identify inefficiencies in the production line, such as bottlenecks or underutilized resources. These insights allow manufacturers to reconfigure the production process to improve throughput and reduce waste.
For example, if a Digital Twin reveals that a particular machine is operating below capacity, manufacturers can adjust its schedule or optimize its usage to increase productivity. Additionally, by simulating different scenarios, manufacturers can test new production strategies without disrupting the physical system, helping to identify the most efficient workflows.
- Faster Time-to-Market
The ability to simulate and test production processes virtually can significantly reduce the time it takes to bring a new product to market. By using Digital Twins to model the manufacturing process, manufacturers can identify and address potential issues early in the design phase. This means that less time is spent on trial and error in the real-world production environment, leading to faster product development cycles.
Moreover, Digital Twins allow manufacturers to simulate different product designs and manufacturing strategies, helping them choose the most efficient approach before investing in physical prototypes. This can lead to quicker iterations, reduced costs, and shorter lead times.
- Energy and Resource Efficiency
Manufacturers always aim and constantly strive to lower energy consumption and minimize waste. Digital Twins help identify opportunities for improving energy efficiency by simulating energy usage and pinpointing areas where resources are being wasted. For instance, by monitoring temperature, humidity, and equipment performance, a Digital Twin can help optimize energy use across the entire production process.
Additionally, Digital Twins can help track material usage, identify inefficiencies, and suggest ways to reduce scrap and waste. This can have a significant impact on a company’s bottom line, as well as its environmental footprint.
- Improved Decision-Making
By providing real-time insights into production processes, Digital Twins enables manufacturers to make more informed and data-driven decisions. Whether it’s identifying trends in machine performance or optimizing supply chain logistics, the data provided by Digital Twins helps managers make smarter decisions that improve the overall efficiency of the operation.
Moreover, Digital Twins can integrate data from various systems, such as ERP (Enterprise Resource Planning), MES (Manufacturing Execution Systems), and SCM (Supply Chain Management), to provide a holistic view of the entire manufacturing process. This integrated view allows manufacturers to streamline their operations and make decisions that improve productivity, reduce costs, and boost profitability.
Challenges in Implementing Digital Twins
While the benefits of Digital Twins in manufacturing are clear, there are several challenges that companies may face when implementing this technology.
- High Initial Investment
One of the primary barriers to adopting Digital Twins is the initial investment required for the technology. Setting up a Digital Twin system involves purchasing sensors, IoT devices, and software, as well as integrating them with existing systems. For small and medium-sized manufacturers, the upfront costs can be significant. However, the long-term benefits, including reduced downtime, improved product quality, and optimized production processes, often outweigh the initial investment.
- Data Management
Digital Twins rely heavily on data to function effectively. Manufacturers need to ensure that they have robust data management systems in place to collect, store, and analyze the vast amounts of data generated by sensors and IoT devices. Proper data governance and cybersecurity measures must also be implemented to protect sensitive information.
- Integration with Existing Systems
Integrating Digital Twins with existing manufacturing systems, such as MES or ERP, can be a complex and time-consuming process. Manufacturers need to ensure that the Digital Twin platform can communicate seamlessly with these systems to provide real-time insights and support decision-making.
- Skilled Workforce
Implementing Digital Twins requires a workforce with expertise in data analytics, machine learning, and other advanced technologies. Manufacturers may need to invest in training or hire new talent to fully leverage the potential of Digital Twins.
Digital Twins are revolutionizing the manufacturing industry by optimizing production and enhancing efficiency. By providing real-time insights, predictive maintenance capabilities, and opportunities for process optimization, Digital Twins helps manufacturers improve productivity, reduce costs, and deliver higher-quality products. Though there are difficulties involved in adopting this technology, the advantages are much greater than the challenges. As Digital Twin technology continues to evolve, its role in transforming the manufacturing sector will only grow, making it an essential tool for manufacturers looking to stay competitive in an increasingly digital world.